Expert Advice on What is Porosity in Welding and Just How to Resolve It
Expert Advice on What is Porosity in Welding and Just How to Resolve It
Blog Article
Porosity in Welding: Identifying Common Issues and Implementing Best Practices for Avoidance
Porosity in welding is a prevalent problem that typically goes unnoticed till it creates considerable problems with the integrity of welds. This usual flaw can jeopardize the strength and resilience of welded structures, posing safety and security dangers and leading to pricey rework. By comprehending the root creates of porosity and applying reliable prevention approaches, welders can substantially improve the top quality and dependability of their welds. In this discussion, we will certainly explore the crucial elements adding to porosity development, examine its destructive effects on weld efficiency, and go over the most effective techniques that can be adopted to decrease porosity incident in welding procedures.
Typical Sources Of Porosity
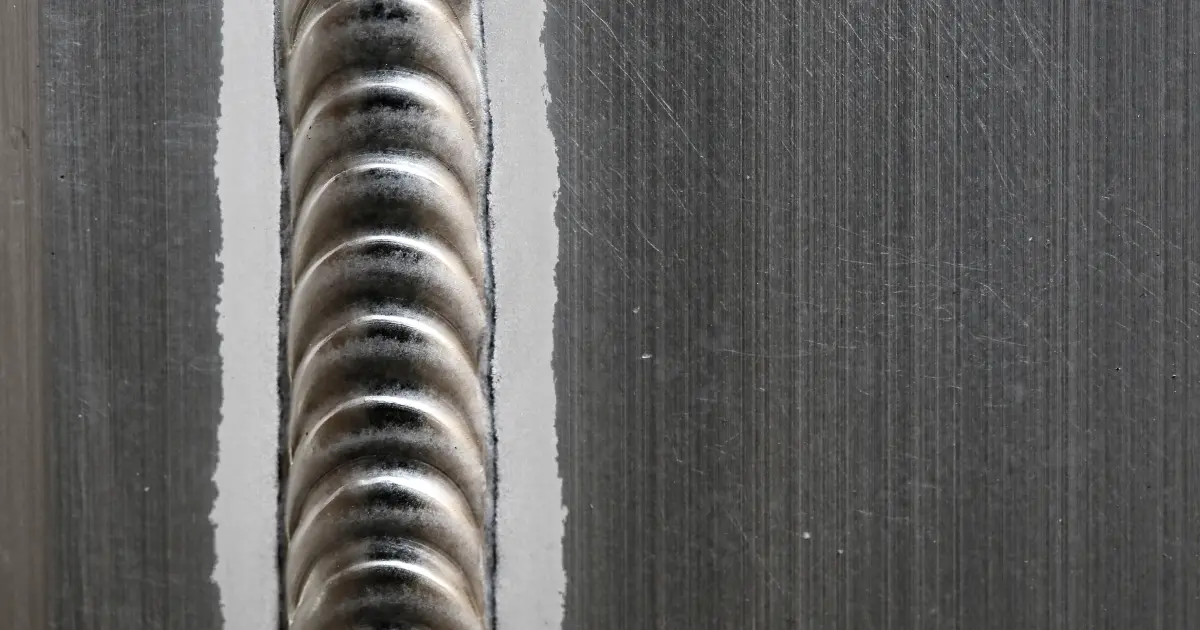
An additional frequent perpetrator behind porosity is the presence of pollutants externally of the base metal, such as oil, grease, or rust. When these contaminants are not effectively eliminated before welding, they can vaporize and become trapped in the weld, causing defects. Using unclean or damp filler materials can introduce impurities right into the weld, adding to porosity problems. To mitigate these common root causes of porosity, thorough cleansing of base steels, appropriate shielding gas selection, and adherence to optimum welding specifications are vital practices in achieving high-grade, porosity-free welds.
Influence of Porosity on Weld High Quality

The presence of porosity in welding can significantly jeopardize the structural stability and mechanical residential properties of welded joints. Porosity produces gaps within the weld steel, compromising its total strength and load-bearing capability. These voids function as stress concentration factors, making the weld more prone to cracking and failure under used tons. In addition, porosity can decrease the weld's resistance to rust and various other environmental aspects, better decreasing its long life and efficiency.
Welds with high porosity degrees have a tendency to exhibit lower impact toughness and lowered capacity to warp plastically before fracturing. Porosity can hinder the weld's ability to effectively send pressures, leading to premature weld failure and possible safety risks in critical frameworks.
Finest Practices for Porosity Prevention
To improve the structural stability and quality of welded joints, what specific procedures can be applied to minimize the incident of porosity throughout the welding process? Porosity avoidance in welding is essential to make sure the integrity and stamina click resources of the last weld. One reliable technique appertains cleaning of the base metal, getting rid of any pollutants such as rust, oil, paint, or dampness that might lead to gas entrapment. Making certain that the welding devices remains in great condition, with clean consumables and suitable gas circulation rates, can additionally substantially reduce porosity. Additionally, keeping a steady arc and regulating the welding parameters, such as voltage, existing, and take a trip rate, helps produce a constant weld swimming pool that reduces the risk of gas entrapment. Utilizing the proper welding method for the details material being welded, such as changing the welding angle and weapon position, can additionally prevent porosity. Routine examination of welds and immediate removal of any kind of issues determined throughout the welding procedure are important methods to avoid porosity and create high-quality welds.
Relevance of Proper Welding Techniques
Applying appropriate welding techniques is vital in guaranteeing the architectural stability and quality of welded joints, building upon the structure of effective porosity prevention measures. Too much warm can lead to raised porosity due to the entrapment of gases in the weld pool. In addition, utilizing the ideal welding specifications, such as voltage, existing, and travel rate, is essential for accomplishing sound welds with very little porosity.
In addition, the choice of welding procedure, whether it be MIG, TIG, or stick welding, ought to line up with the specific demands of the task to ensure ideal outcomes. Proper cleaning and prep work of the base steel, as well as choosing the appropriate filler material, are likewise important elements of skillful welding techniques. By adhering to these finest techniques, welders can minimize the danger of porosity development and generate top quality, structurally sound welds.

Evaluating and Quality Assurance Measures
Quality control actions play a vital duty in verifying the integrity and dependability of bonded joints. Examining treatments are necessary to discover and protect against porosity in welding, ensuring the strength and toughness of the end product. Non-destructive testing methods such as ultrasonic testing, radiographic testing, and aesthetic assessment are frequently used to recognize possible issues like porosity. These techniques allow for the assessment of weld high quality without jeopardizing the honesty of this hyperlink the joint. What is Porosity.
Carrying out pre-weld and post-weld evaluations is also essential in preserving quality control criteria. Pre-weld assessments involve validating the materials, tools setups, and sanitation of the workplace to avoid contamination. Post-weld examinations, on the other hand, analyze the final weld for any type of problems, consisting check this site out of porosity, and confirm that it meets specified requirements. Executing a thorough quality assurance plan that includes complete screening procedures and evaluations is extremely important to reducing porosity concerns and ensuring the overall top quality of welded joints.
Final Thought
To conclude, porosity in welding can be a typical issue that impacts the high quality of welds. By identifying the typical reasons of porosity and implementing best methods for prevention, such as correct welding strategies and testing measures, welders can ensure top quality and dependable welds. It is important to focus on avoidance techniques to reduce the occurrence of porosity and maintain the honesty of welded structures.
Report this page